Start by cutting off a desired length of guitar cable. The recommended temperature for this kind of work is 350 degrees Celsius. If you’re still a bit unsure about your soldering skills, you could drop the temperature down to 300 C. Seasoned soldering professionals can use higher settings.

It is very important to solder in a room with sufficient ventilation. Soldering tin contains some lead, which you don’t want to breathe in. Use a table fan blowing across the table/workbench at an angle – you want the air to circulate, without the fan blowing straight on the solder joints.
The basic idea behind soldering is not just to solder the cable and the component together with tin, but pre-tinning the soldering lug and the conductor strand first, and then connect the tinned surfaces together using heat iron. Understanding this is crucial if you want to make solid connection. The ideal practice for making the joint is to heat the components and let the tin melt on their surface and try not to touch tin with your iron tip. This can be tricky, because too much heat in the components can make cable insulations melt.
The second important factor for achieving a good solder joint is keeping cable and component perfectly still until the tin is completely cooled off. Do not blow on the hot connection to make it cooler as it will ruin your nicely made solder joint. Try also not to overheat any surface – if you have trouble with a certain solder joint, take a break of a couple of minutes and return to the joint once the surface has cooled off. Too much heat can also lead to component failure or shorts, which might lead to other problems further down the line.
Remember, the tip of a soldering iron stays very hot for some time after switching off your soldering station, so be careful when laying it back to its holder.
Custom Boards uses Neutrik-plugs for all their guitar cables. The board-facing end of a guitar lead will always be equipped with an angled plug, but the plug for the guitar can be either. Most Gibson guitars tend to work better with angled plugs, while guitars like the Fender Stratocaster will require straight plugs.
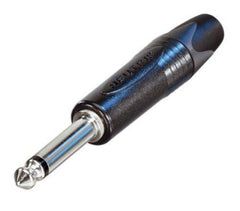

- Feed the cable through the Neutrik’s black plastic back cover.
- For a straight Neutrik-plug take off about one centimetre, for an angled Neutrik strip off 2-3 cm.
- Take the outer copper mesh (ground/earth) to one side of the cable and twirl it into a braid.
- Remove the black graphite foil around the hot conductor. You can do this with a fingernail, or by very careful use of a knife or wire stripper.
- Tin all stripped conductor ends quickly and decidedly. The soldering iron’s tip should only touch the conductor’s stripped off surface. Heat the copper for about two seconds and touch the surface with your tin. The tin should start to flow immediately. Quickly remove the iron and let the conductor cool off without moving the cable.
- You can use an old effect pedal or DI-box as a third hand, simply by plugging the disassembled plug in. If you’re planning on soldering dozens of plugs, you could even use a battered old patch bay – or any other unused piece of equipment with lots of jack sockets – for the job.
- After this phase it is advisable to do a mock-fitting of the soldered joints. Bend the tinned ends of the lead until they sit nicely on the lugs. Plan carefully in which order you will solder the joints.
- Cut the ground so short that it is impossible for it to touch the tip causing a short.
- If you have stripped and tinned the tip too long, now would be a good time to cut it to size and to make sure it will reach its corresponding lug.
- Tin the plug’s soldering surfaces/lugs. If possible, heat the soldering contacts from the opposite side from where you put your soldering tin. Heat the plug’s contacts for two to three seconds before applying the tin. The tin should melt instantly, and you should remove the iron quickly.
- Join the cable and plug together using the heat iron. Don’t screw on the plug’s cover just yet, keep on soldering until all cables have been joined to their plugs.
- Generally it’s best to first solder the tip in the middle, wait for it to cool down and then guide the ground in its place with the lead and solder it in its lug. If you have done the mock-fitting beforehand, the ground should reach the lug exactly when you bend the lead down. This way you don’t have to put your fingers near the solder risking a burn.

Repeat all necessary steps for the plugs at the other end of your loom. Here is the similar procedure for the angled plug.




- Turn off your soldering iron, and put it into its stand to cool off.
- Tighten the black plastic back covers, which are part of a Neutrik-plug’s strain relief. Use the company’s gray special tool for this job, which is a good investment, if you plan on making more cables. Otherwise, I’d recommend using thin gloves to give you the necessary torque.


*****
If you have purchased all the parts and components but get a feeling that you might not be up to the task after all, we can make your pedalboard for you, using the components you have bought from us. Don’t worry, we won’t let anything go to waste.
START BUILDING YOUR PEDALBOARD TODAY.
See our services